3D printing helps green casting
2025-01-24 10:18:48 hits:0
In the process of the casting industry's move towards green and sustainable development, 3D printing technology, with its unique advantages, is gradually becoming a key force driving the development of green casting. 3D printing technology, also known as additive manufacturing technology, is different from traditional manufacturing processes. It manufactures objects by layer - by - layer material deposition based on three - dimensional model data. This technology provides strong impetus for the development of green casting from multiple dimensions.
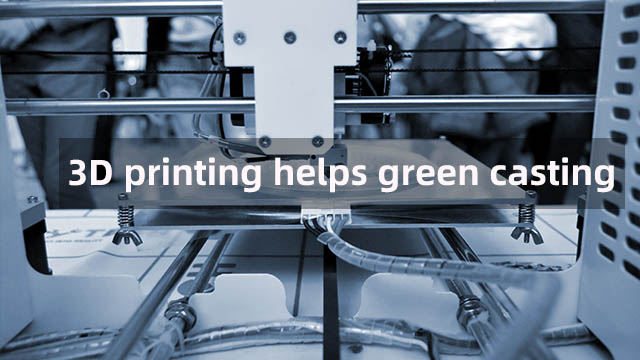
Significantly Reducing Material Waste
In the traditional casting process, a large amount of raw materials often need to be cut and processed, resulting in a considerable amount of waste. For example, when manufacturing complex - shaped automotive parts, a large amount of metal materials are removed during the processing, causing waste of resources. However, 3D printing technology manufactures by layer - by - layer material deposition, accurately supplying materials according to the actual shape and size of the parts, with almost no excess waste. Taking the manufacturing of aero - engine blades as an example, the material utilization rate of traditional casting processes may only be 30% - 40%, while with 3D printing technology, the material utilization rate can be increased to over 80%. This greatly reduces the consumption of raw materials, reduces the environmental burden and cost expenditure caused by material waste, and conforms to the concept of efficient resource utilization in green casting.
Achieving Precise Casting of Complex Structures
Green casting pursues high - performance and lightweight products, which requires castings to have complex and sophisticated structures. 3D printing technology is not limited by the molds and processing methods in traditional manufacturing processes and can easily achieve the casting of complex structures. For example, lattice structures have excellent mechanical properties and lightweight characteristics, but they are difficult to manufacture by traditional casting processes. Through 3D printing technology, such complex lattice structures can be accurately constructed and applied to the manufacturing of automotive engine cylinder blocks, lightweight body components, etc. These complex structures not only improve the performance of components, such as enhancing the strength and heat - dissipation performance of components, but also achieve lightweight design, reducing the overall weight of the vehicle, thereby reducing energy consumption and exhaust emissions, and promoting the development of green casting in terms of product performance improvement and environmental protection.
Reducing Energy Consumption
In traditional casting processes, mold manufacturing, casting processing, and other links consume a large amount of energy. The mold - manufacturing process is complex and requires multiple processes, consuming a large amount of electricity and other energy sources. However, 3D printing technology does not require mold manufacturing and directly prints according to the design model, reducing the energy consumption in the mold - manufacturing process. At the same time, since 3D printing can achieve one - step forming, subsequent processing procedures are reduced, further reducing the overall energy consumption. Research shows that compared with traditional casting processes, in the manufacturing of some specific parts, 3D printing technology can reduce energy consumption by 30% - 50%, making an important contribution to the energy - conservation and emission - reduction goals of green casting.
Accelerating Product R & D and Innovation
The development of green casting is inseparable from continuous product research and development and innovation. 3D printing technology can quickly transform design concepts into physical models, greatly shortening the product R & D cycle. When developing new automotive parts, engineers can use 3D printing technology to quickly produce samples for performance testing and optimized design. Through repeated rapid iterations, high - performance products that meet the requirements of green casting can be developed more quickly. For example, when developing new aluminum - alloy automotive wheels, 3D printing technology is used to quickly manufacture samples with different structures and material ratios. After testing and analysis, the optimal design plan is determined, accelerating the R & D process of new wheels and promoting the innovation and development of green - casting products.
With its outstanding performance in reducing material waste, achieving complex - structure casting, reducing energy consumption, and accelerating product R & D and innovation, 3D printing technology has injected strong impetus into the development of green casting. With the continuous progress of 3D printing technology and the gradual reduction of costs, its application prospects in the field of green casting will be even broader, and it is expected to lead the casting industry to move forward vigorously in a more green, efficient, and innovative direction.
As a leading enterprise in the industry, Tiegu has been actively exploring the in - depth integration of 3D printing technology and green casting. By introducing advanced 3D printing equipment and technical talents, Tiegu has achieved remarkable results in the green casting production of complex parts. It has not only successfully achieved a significant increase in material utilization rate and effective reduction in energy consumption but also led the industry in product R & D speed. Tiegu sincerely looks forward to working hand in hand with partners from all sectors to jointly explore more potential of 3D printing technology in green casting and create a new future for green casting.