Five Advantages of Green Casting in Reducing the Production Cost of Automobile Parts
2025-01-24 09:35:20 hits:0
In the current booming automotive industry, controlling production costs is one of the key factors for automotive enterprises to enhance their market competitiveness. Green casting, as an advanced casting mode, not only conforms to the environmental protection concept but also opens up new paths for reducing the production costs of automobile parts.
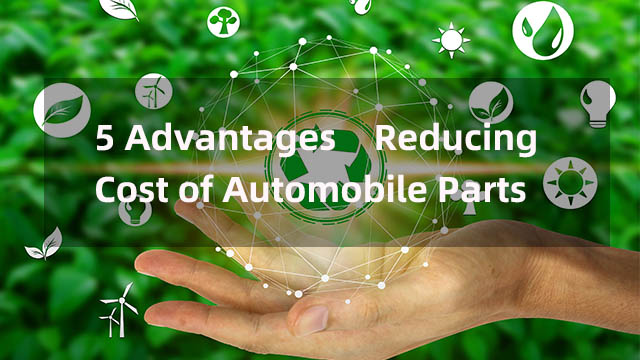
Green Design Optimizes the Cost Foundation
Green design is the starting point of green casting and is of great significance for automobile parts. During the design stage, engineers can use computer - aided design (CAD) technology to perform topological optimization on parts. For example, in the design of an automobile engine cylinder block, through simulation analysis, the parts with less stress in the structure are removed. On the premise of ensuring the strength and performance of the cylinder block, lightweight design is achieved, reducing the amount of materials used. At the same time, the modular design concept is adopted, and automobile parts are divided into different modules according to functions, such as the skeleton and adjustment mechanism modules of automobile seats. In this way, during production, different modules can be cast separately according to requirements, improving production efficiency. Moreover, during the later maintenance or upgrade of the product, it is convenient to disassemble and replace a single module, reducing maintenance costs and overall replacement costs.
Green Materials Reduce Comprehensive Costs
Selecting appropriate green materials can reduce the production costs of automobile parts in many aspects. The use of new - type environmentally friendly binders may have a slightly higher initial purchase cost than traditional binders. However, in the long run, since they do not contain harmful substances, the investment and operation costs of environmental protection equipment such as ventilation and waste gas treatment in the production workshop are reduced. At the same time, recyclable metal materials, such as recycled aluminum alloy, are relatively cheaper than primary aluminum alloy. When automobile wheels are cast with recycled aluminum alloy, not only the raw material procurement cost is reduced, but also the energy consumption and environmental governance costs in the processes of primary metal mining and smelting are reduced. These cost reductions are ultimately reflected in the total product cost.
Green Processes Improve Production Efficiency
Advanced green casting processes have a direct and significant impact on reducing the production costs of automobile parts. Precision casting processes, such as investment casting, are widely used in the production of automobile parts. For example, the impeller of an automobile engine turbocharger can be directly cast into a complex shape by investment casting, with high dimensional accuracy and low surface roughness. The subsequent processing allowance can be reduced by more than 80%. This greatly reduces the machining time and processing cost, as well as the tool wear and energy consumption of processing equipment. In addition, computer simulation technology is used to conduct simulation analysis on the filling and solidification processes before casting, predict possible defects in advance, such as shrinkage cavities and porosity, optimize process parameters, and improve the product qualification rate, avoiding cost waste caused by the generation of defective products.
Resource Recycling Creates Additional Value
A large amount of waste, such as waste sand and waste metal, is generated during the casting process of automobile parts. Effective resource recycling of these wastes can reduce costs. Waste sand is processed through regeneration processes such as mechanical methods and thermal methods and is reused for molding, replacing part of the new sand and reducing the new sand procurement cost. Taking a casting factory that produces 100,000 automobile brake discs annually as an example, if the waste sand regeneration utilization rate reaches 80%, hundreds of thousands of yuan in new sand procurement costs can be saved every year. For waste metal, after classification and recycling, it is remelted and used to produce automobile parts with lower added value or as a supplement to the furnace charge of the smelting furnace, realizing resource recycling and reducing raw material costs.
Energy Conservation and Emission Reduction Reduce Operating Costs
The energy - conservation and emission - reduction measures of green casting help to reduce the operating costs of automobile parts production enterprises. Using high - efficiency and energy - saving furnaces, such as medium - frequency induction furnaces to replace traditional resistance furnaces, can increase the thermal efficiency by 20% - 30%, reducing the energy consumption cost. The waste heat recovery system is used to use the waste heat of high - temperature flue gas generated during the casting process to preheat metal charges or heat the production workshop, reducing the dependence on external energy. According to statistics, a medium - sized automobile parts casting enterprise can save hundreds of thousands of yuan in natural gas or electricity costs every year after implementing waste heat recovery.
Green casting provides a comprehensive and effective solution for reducing the production costs of automobile parts through various measures such as green design, green materials, green processes, resource recycling, and energy conservation and emission reduction. Tiegu, as a pioneer enterprise in the industry focusing on green casting, has rich experience in the green casting of automobile parts and owns advanced technical equipment and a professional R & D team. Tiegu can accurately control all aspects of green casting, from design optimization to material selection, from process innovation to resource recycling, and comprehensively assist automobile parts production enterprises in reducing costs and enhancing product competitiveness. We look forward to working hand in hand with a large number of enterprises related to the automotive industry to jointly promote the wide application of green casting in the production of automobile parts and achieve mutual benefit and win - win results.
Previous: What is green casting?