Causes des gros grains dans les pièces moulées pendant la production
2024-11-25 15:37:34 hits:0
Les gros grains dans les pièces moulées sont un phénomène courant mais indésirable qui a un impact direct sur les propriétés mécaniques et la durée de vie des pièces moulées. Comprendre les causes des gros grains est crucial pour optimiser les processus de production et améliorer la qualité de la coulée. S'appuyant sur de nombreuses années de pratique de production et de références à des matériaux pertinents, l'auteur explorera les causes possibles de la présence de gros grains dans les pièces moulées sous de multiples aspects.
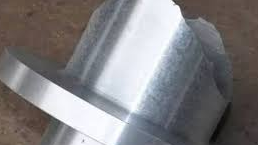
1.Impact de la composition de l'alliage
- Teneur excessive en carbone: Une teneur élevée en carbone dans les pièces moulées en acier peut entraîner une précipitation de carbure, réduisant les taux de nucléation et accélérant la croissance des grains.
- Éléments d'alliage insuffisants: Les oligo-éléments comme le titane et le vanadium contribuent à affiner les grains. Un manque de ces éléments peut entraîner la formation de grains grossiers.
- Influence des impuretés: Les impuretés telles que le soufre et le phosphore forment des zones ségréguées à bas point de fusion, conduisant à un grossissement localisé des grains.
2. Contrôle inapproprié du taux de refroidissement
- Refroidissement lent: Un taux de refroidissement plus lent donne aux grains plus de temps pour croître, ce qui donne lieu à des structures plus grossières.
- Dégradés de refroidissement inégaux: Les différences de vitesse de refroidissement entre les sections peuvent provoquer des grains grossiers localisés.
- Conception de moule déficiente: Une conductivité thermique inégale du moule ou un contrôle inapproprié de la température dans les moules peuvent indirectement contribuer à un refroidissement irrégulier.
3. Surchauffe ou temps de fusion prolongé
- Température de fusion excessive: Des températures plus élevées favorisent la croissance des grains et peuvent brûler des oligo-éléments, réduisant ainsi les sites de nucléation.
- Temps de maintien prolongé: Des périodes de maintien prolongées donnent aux grains plus de temps pour pousser, surtout sans une agitation suffisante.
4. Autres problèmes liés au processus de casting
- Température de préchauffage excessive du moule: Des températures de préchauffage élevées retardent le refroidissement, conduisant à des grains grossiers.
- Vitesse de versement rapide: Un versement rapide peut provoquer des turbulences, réduisant la nucléation et formant des zones de grains grossiers.
- Défauts métallurgiques non traités: Les inclusions et la porosité des gaz diminuent la densité des sites de nucléation efficaces, contribuant ainsi à des grains plus grossiers.
5. Manque de raffinement des grains
- Absence de raffineurs de grains: Des éléments comme le bore, le strontium et le manganèse raffinent efficacement les grains, et leur mauvaise utilisation ou leur manque d'utilisation peut entraîner des grains plus grossiers.
- Agitation insuffisante: Une mauvaise répartition des agents d'affinage ou une agrégation de particules dans la masse fondue peut nuire au raffinement des grains.
6. Traitement thermique inapproprié
- Température ou durée de recuit excessive: La croissance des grains se produit pendant le traitement thermique, et un traitement excessif exacerbe le grossissement des grains.
- Refroidissement rapide incontrôlé et chauffage lent: Si les vitesses de refroidissement et de chauffage sont mal maîtrisées, les grains peuvent croître anormalement.
Les causes des céréales secondaires impliquent une combinaison de composition des matériaux, de conception des processus, d’équipement et de pratiques opérationnelles. Résoudre ces problèmes nécessite une analyse minutieuse et une élimination étape par étape. En contrôlant la composition de l'alliage, en optimisant les taux de refroidissement, en gérant avec précision les températures et les durées de fusion, en concevant de meilleurs processus de coulée et en adoptant des techniques avancées de raffinement des grains, la formation de grains grossiers peut être efficacement minimisée, améliorant ainsi les performances globales des pièces moulées.