Application de la fonte ductile dans les rails à grande vitesse
2024-12-23 12:06:51 hits:0
I. Application de la fonte ductile dans les trains à grande vitesse
Les pièces moulées en fonte ductile, avec leur excellente résistance à la traction et à la limite d'élasticité, leur bonne résistance aux chocs et à la rupture, leur résistance exceptionnelle à l'usure et à la corrosion, ainsi que leur capacité à supporter des charges et des frottements élevés, sont largement utilisées dans la production de rails à grande vitesse. composants.
Les boîtes d'essieux des bogies ferroviaires à grande vitesse, les carters et les couvercles d'extrémité des moteurs de traction ferroviaire à grande vitesse, ainsi que les carters de boîtes de vitesses et les composants de frein des trains à grande vitesse sont tous des pièces moulées en fonte ductile résistante aux chocs à ultra-basse température. Généralement, ils sont fabriqués à partir de matériaux QT400 - 18AL (-50 °C, -60 °C) résistant aux chocs à basse température.
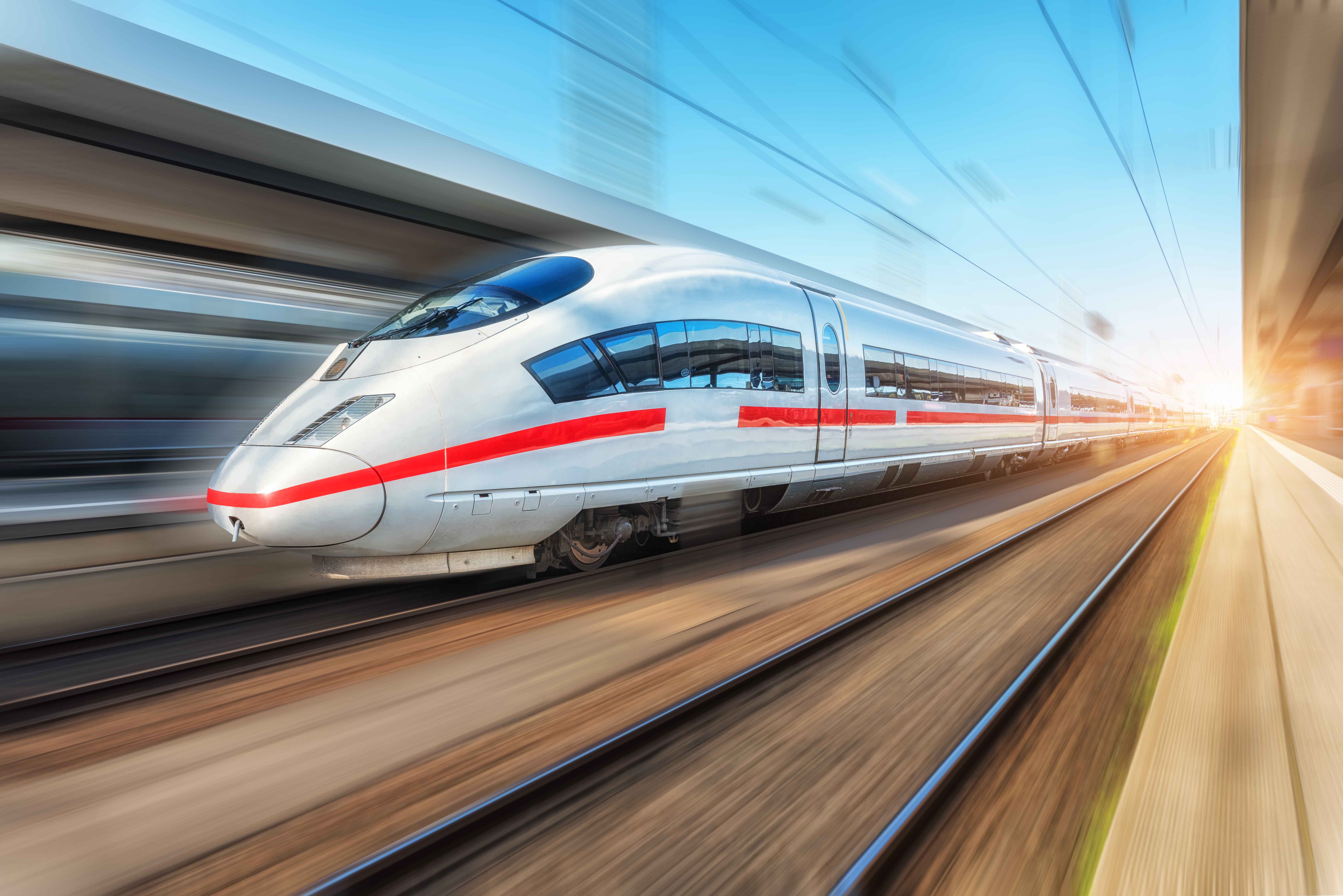
II. Normes de matériaux pour les composants en fonte ductile des rails à grande vitesse
QT400 - 18AL (-50 °C, -60 °C) matériau résistant aux chocs à basse température, exigences matérielles :
- Norme matérielle : 400 - 18AL
- Résistance à la traction : ≥ 400 Mpa
- Limite d'élasticité : ≥ 240 Mpa
- Allongement : ≥ 18%
- Dureté HBW : 130 - 150
- Valeur d'impact à basse température : -50 °C, -60 °C.
- Énergie d'impact : 12 J/cm²
- Exigences relatives à la structure de la matrice métallographique :
- Taux de sphéroïdisation : supérieur à 90 %
- Nombre de nodules de graphite : ≥ 100 nodules/mm²
- Structure matricielle : 100 % ferrite
- Taille du graphite : grades 6 à 7
- Sans eutectique de phosphore ni carbure
Une matrice 100 % ferrite est la condition principale pour améliorer la valeur d’impact à basse température de la fonte ductile. Même 1 à 2 % de perlite entraînera une diminution de la valeur d'impact à basse température. Pour la fonte ductile ferrite, la fonte ductile pleine ferrite recuite à faible teneur en phosphore et à faible teneur en silicium présente la meilleure valeur d'impact à basse température.
Un taux de sphéroïdisation de 90 % à 95 % est une condition nécessaire pour garantir la valeur d’impact à basse température. Les fissures dans la fonte ductile s'étendent le long des limites des nodules. Plus les nodules sont ronds, moins les fissures risquent de se produire. Par conséquent, plus le taux de sphéroïdisation est élevé, plus il est bénéfique pour l’amélioration des performances aux chocs, de la résistance à la fatigue et d’autres performances de charge dynamique.
L'influence du nombre de nodules de graphite sur l'impact à basse température : un petit nombre de nodules de graphite est bénéfique pour améliorer la limite supérieure des performances d'impact ; un grand nombre de nodules de graphite est bénéfique pour améliorer les performances d'impact à basse température. Pour les boîtes d'essieux de bogies avec une épaisseur de paroi principale de 30 mm, 100 à 200 nodules/mm² sont appropriés. L'eutectique du phosphore et le carbure aux joints de grains réduiront considérablement l'énergie d'absorption d'impact à basse température de la fonte ductile.
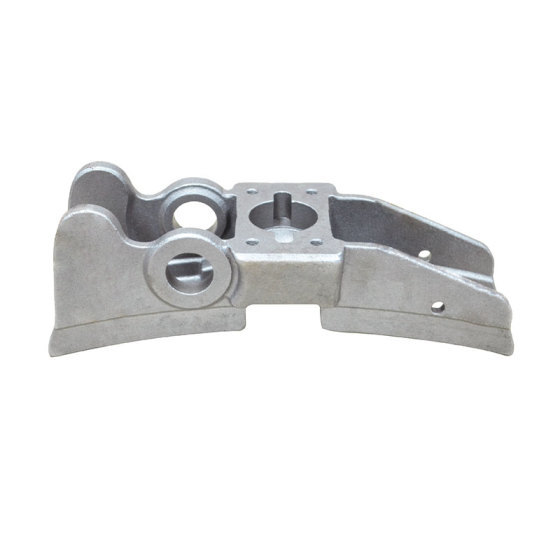
III. Processus de production de boîtes d'essieux en fonte ductile pour rails à grande vitesse
1. Exigences relatives au fer fondu brut
Composition chimique du fer brut en fusion avant réaction de sphéroïdisation :
- C : 3,9 % - 3,98 %
- Si : 0,65 % - 0,75 %
- En : 0,75% - 0,83%
- Mn : ≤ 0,10 %
- P : ≤ 0,025 %
- S : ≤ 0,015 %
- Si : ≤ 0,015%
- Cr : ≤ 0,015 %
- Autres alliages traces : ≤ 0,01 %
Le niveau de teneur en Si affecte directement la résistance à la traction et la valeur aux chocs ; lorsque la réduction de Si ne peut pas répondre aux exigences de résistance, la méthode d'ajout de Ni est utilisée pour résoudre le problème de résistance insuffisante provoquée par la réduction de Si. (Ni est ajouté dans ce plan)
2. Matières premières
- Fonte brute : Utilisation de fonte brute de haute qualité fournie par Tiegu. Le contrôle total des oligo-éléments dans la composition chimique de la fonte ≤ 0,10%.
- Ferraille d’acier : de la ferraille d’acier au carbone est utilisée.
- Toute ferraille d’acier ne doit pas être mélangée à de la saleté. Métaux non ferreux ou tout type de matériaux étrangers, et il ne doit pas y avoir de rouille ni de corrosion excessives.
- Les teneurs en P et S ne dépassent pas toutes deux 0,030 %.
- La fraction massique de Cr n'est pas supérieure à 0,1 %.
- La fraction massique de Cu n'est pas supérieure à 0,1 %.
- Carburateur : Carburateur entièrement graphité haute température, C ≥ 98,5 %, S ≤ 0,1 %, N ≤ 0,03.
Lors de la formulation du mélange, davantage de fonte brute est utilisée, moins de ferraille d'acier et de ferraille de retour sont utilisées, et le calcul est effectué pour être aussi proche que possible de la composition chimique idéale, laissant un petit espace de réglage fin. Le but de l'ajout de plus de fonte brute est de garantir le nombre de noyaux de graphite d'origine, tout en réduisant la quantité de carburateur ajoutée et l'augmentation de soufre provoquée par le carburateur. Une formule courante est que la fonte brute représente 88 % à 92 %, la ferraille d'acier représente 8 % à 11 %, le ferrosilicium représente 1,7 % à 2,0 % et les carburateurs représentent 0,2 % à 0,24 %.
- Agent sphéroïdisant :
- Marque: Agent sphéroïdisant lanthanide La - 1
- MG : 6 - 6,5 %
- Le : 1,0 - 1,2 %
- Et : 43 - 44 %
- CA: 2,2 - 2,5%
- BA: 1 - 1,5%
- MGO: <0,5
- Granularité: 5 - 20 mm
- Montant d'addition: 1,2 - 1,3%
- Inoculant: un inoculant composite à action prolongée est utilisé.
- Inoculation primaire: Silicon Barium J - 4
- Si: 68 - 70%
- BA: 4,5 - 5,5%
- Al: <1,0%
- Granularité: 3 - 8 mm
- Montant d'addition: 0,8 - 1,0%
- Inoculation secondaire: Silicon Barium J - 3
- Si: 68 - 70%
- BA: 2,5 - 3,5%
- Al: <1,0%
- Granularité: 1 - 3 mm
- Montant d'addition: 0,2 - 0,4%
- Inoculation de tundish: Silicon Bismuth J - 1
- Si: 70 - 72%
- BA: 1 - 1,5%
- CA: 2 - 3%
- BI: 1,5 - 2,5%
- Al: <0,8%
- Granularité: 0,2 - 0,7 mm
- Montant d'ajout: 0,1%
L'inoculant est nécessaire pour avoir un fort effet favorisant du graphite, peut maintenir longtemps et a un taux d'absorption élevé et stable. Par conséquent, l'inoculation est divisée en inoculation avant du four, inoculation de la louche et inoculation du tundish, qui sont toutes indispensables.
À l'avant du four, un inoculant anti-BA anti-dépasse et à longue durée est utilisé, et pendant la coulée, un inoculant contenant du bif. Petit, le nombre de nodules importants et l'augmentation de la teneur en ferrite et l'amélioration des performances telles que couchées.
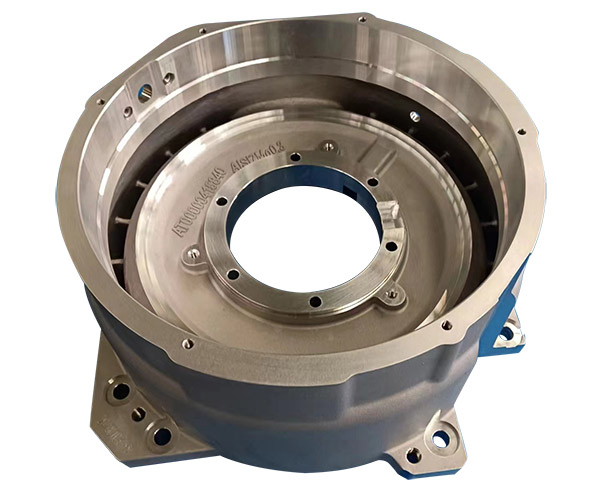
3. Processus de fusion
Le processus de fusion du fer ductile est fondamentalement le même. La température de fusion est généralement contrôlée de 1450 à 1520 ° C, debout à haute température, la température est contrôlée à 1520 à 1550 ° C, le temps debout est d'environ 5 minutes, la température de taraudage est de 1480 à 1500 ° C et la température de versement est de 1420 ° C.
Une fois debout à haute température, lorsque la température du four chute à 1480 ° C - 1500 ° C, le fer fondu est tapé et le traitement de sphéroïdisation est effectué. Une fois la réaction sur le point de se terminer, le laitier est retiré 2 à 3 fois.
4. Composition chimique après réaction de sphéroïdisation
- C: 3,50 - 3,80%
- Si: 2,05 - 2,15%
- Mg: 0,035 - 0,045%
- LA: 0,005 - 0,009%
- Dans: 0,75 - 0,83%
- Mn : ≤ 0,10 %
- P : ≤ 0,025 %
- S: ≤ 0,01%
- Si: ≤ 018%
- CR: ≤ 0,023%
- Autres éléments d'alliage: ≤ 0,01%
Résistance à la traction: 405 - 415 PMA
Force d'élasticité: 260 - 275 PMA
Allongement: 18% - 23%
Grade de sphéroïdizon: 1 - 2
Énergie d'absorption d'impact: 13 - 15 J
Tous répondent aux exigences techniques de ce matériel de marque.
Iv. Points clés du traitement de la sphéroïdisation de l'inmersion
Il faut s'assurer que les agents sphéroïdisants sélectionnés, les inoculants, etc. sont purs et exempts d'inclusions, d'impuretés, d'oxydes, etc.
- La fluctuation de la température du traitement des sphéroïdisation est contrôlée à ± 15 ° C.
- Utilisez une louche avec un barrage. Le rapport de la profondeur h de la louche au diamètre intérieur ∮: H: ∮ ≥ 1,5 - 2.0 (la profondeur réelle du fer fondu et le diamètre intérieur pendant le traitement).
- Après avoir ajouté des agents sphéroïdisants, des inoculants, des agents couvrant et d'autres matériaux en utilisant le traitement de type barrage, le barrage doit être d'au moins 20 mm de plus.
- Les louches sont utilisées alternativement. Avant utilisation, les louches sont soigneusement séchées et, si nécessaire, elles sont préchauffées.
- L'ordre d'emballage est l'agent sphéroïdisant, l'inoculant, et le haut est recouvert d'un agent de revêtement ou de limants de fer, qui doivent être tamponnés pour ne laisser aucune lacune.
- Généralement, le temps de réaction optimal pour la sphéroïdisation est de 1 à 1,5 minutes. Ajustez la compacité de l'alliage et l'épaisseur du matériau de revêtement en fonction du temps de réaction.
- L'inoculant couvrant l'agent sphéroïdisant représente 40 à 60% du total (tous les inoculants ajoutés), l'inoculant Ladle représente 30% et l'inoculant de tundish représente 10 à 15%.
- Le temps de versement, de la fin de la sphéroïdisation à la fin, est contrôlé en 13 minutes.
V. Traitement thermique à haute température
Pour produire du QT400 - 18Al (-50 ° C, -60 ° C) un matériau d'impact à basse température, la teneur en ferrite de la matrice doit être à 100%. Étant donné qu'une certaine quantité de Ni est ajoutée pour augmenter la résistance, une trace de perlite sera inévitablement produite. Le but du traitement thermique à haute température est de convertir complètement la perlite en austénite, puis de refroidir lentement selon la transformation de phase stable pour atteindre la transformation complète de la perlite en ferrite, afin d'atteindre une matrice de ferrite 100%.
Grâce à un traitement thermique à haute température à 870 ° C, il y a un impact sur la résistance à la traction, la limite d'élasticité et l'énergie d'absorption d'impact, mais il n'y a aucun impact sur l'allongement. 870 ° C Le traitement thermique à haute température réduit la résistance à la traction de 5 MPa, mais augmente l'énergie d'absorption d'impact de 3 J, ce qui peut répondre aux exigences. Par conséquent, lors de la production de CS400 - 18Al (-50 ° C, -60 ° C) des moulages de matériaux à faible température, un processus de traitement thermique à haute température de 870 ° C est adopté.
Vi. Précautions
- Une matrice de ferrite à 100% est nécessaire pour assurer la valeur d'impact à basse température, mais 100% de ferrite est difficile pour assurer une résistance à la traction de 400 MPa. Il est nécessaire d'effectuer un renforcement de la solution solide sur sa matrice pour améliorer la résistance à la traction. Cela nécessite l'utilisation d'une teneur en SI relativement élevée dans la composition chimique ou l'ajout d'éléments d'alliage tels que Ni pour renforcer la ferrite pour répondre aux exigences de 400 MPa.
- Le renforcement de la ferrite entraîne souvent une augmentation de la température de transition ductile-Brittle et une diminution de la valeur d'impact à basse température. Par conséquent, il est nécessaire d'ajuster la relation entre la résistance à la traction et la valeur d'impact à basse température, qui se restreint mutuellement et explorer les solutions.
- Lorsque la structure métallographique est relativement parfaite et répond essentiellement aux exigences, pour améliorer davantage la valeur d'impact à basse température dépend de la purification des inclusions des frontières des grains. À l'heure actuelle, comment purifier les joints de grains sera le facteur clé pour assurer la valeur d'impact à basse température.
- Les performances d'impact du fer ductile diminuent avec la diminution de la température, qui est une caractéristique inhérente du fer ductile. Pour garantir le fonctionnement sûr des pièces à basse température, non seulement la valeur d'impact à basse température doit être assurée, mais aussi la courbe de température de transition ductile-Brittle, c'est-à-dire la courbe de valeur d'impact changeant avec la température, doit être étudiée. Plus la courbe est plate, plus elle est sûre. Une grande fluctuation de la valeur d'impact causée par un léger changement de température n'est pas recommandée.
Si vous avez des demandes de castings de composants de rail à grande vitesse, vous êtes invités à contacter Tiegu. Tiegu est spécialisée dans la production et la fourniture de divers types de pièces moulées en fer ductile et de moulages en fer gris de différentes marques. Nos produits comprennent des pièces moulées à vide à vide, des pièces moulées pour le rail à grande vitesse, des machines agricoles, des pièces automobiles, des matériaux de construction, etc. Nous fournissons aux clients mondiaux des solutions globales et des services à guichet unique pour la formation et le traitement des métaux.Cliquez pour afficher les produits de coulée.