Agricultural Castings: Quality, Selection & Performance
2025-04-27 16:29:39 hits:0
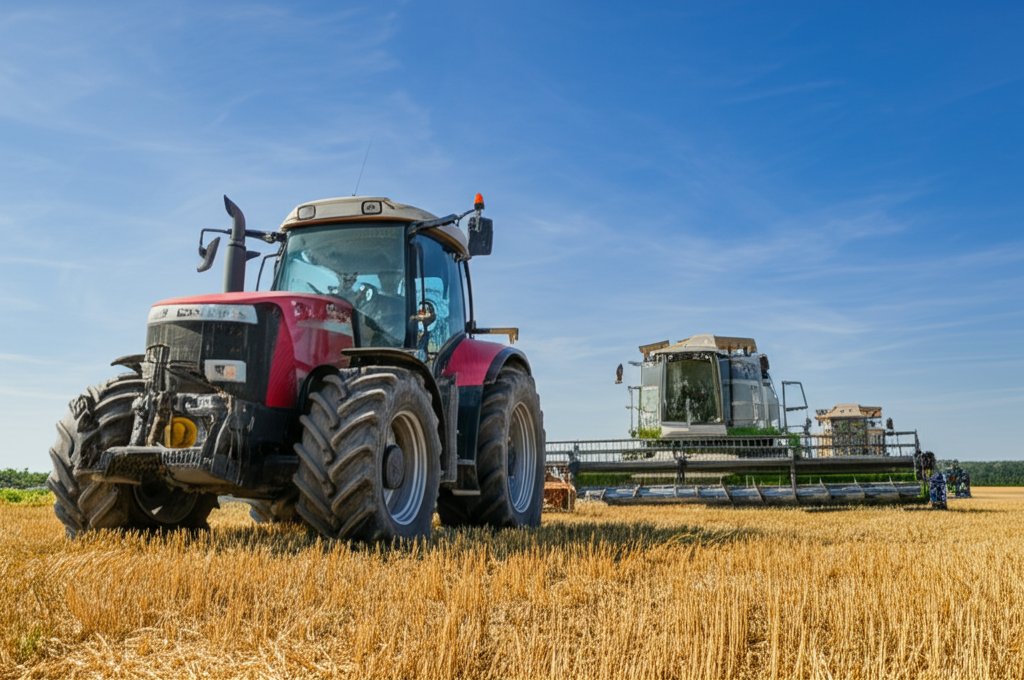
Why Agricultural Castings Are the Backbone of Modern Farming
When you picture a tractor plowing through tough soil or a harvester working nonstop during peak season, have you ever wondered what keeps these machines running reliably? The answer often lies in the quality of their core components—specifically, agricultural castings. These are the custom-shaped metal parts created through casting processes, designed to withstand the demanding conditions of modern agriculture. But what makes them so essential, and why should buyers pay close attention to their quality?
What Are Agricultural Castings and Why Do They Matter?
Agricultural castings refer to metal parts formed by pouring molten metal into shaped molds, then allowing it to solidify. This method is widely used for producing complex, high-strength components found in farm machinery—think housings, brackets, levers, gearboxes, and more. These parts must endure constant vibration, impact, and exposure to harsh environments, making their durability and precision non-negotiable for farmers and equipment manufacturers alike.
Efficiency: High-quality agricultural castings reduce machine downtime, keeping operations running smoothly during critical planting or harvesting windows.
Durability: Precision-engineered castings resist wear, corrosion, and fatigue, extending the lifespan of machinery and lowering replacement costs.
Reliability: Consistent, well-made castings help prevent unexpected breakdowns, safeguarding productivity and profitability on the farm.
Imagine the impact of a single faulty part: a broken gearbox or worn-out housing can bring an entire operation to a halt, leading to lost time and higher expenses. That’s why casting quality is directly tied to operational success.
What Will This Article Cover?
To help you make informed decisions, this guide explores:
What agricultural castings are and how they’re used in farm machinery
Key materials—such as iron and steel alloys—that influence performance
Manufacturing processes like investment and sand casting
Typical applications across tractors, harvesters, and tillage equipment
How to select the right supplier and ensure casting quality
Whether you’re an equipment manufacturer, OEM, or a large-scale grower, understanding the connection between casting quality and equipment reliability can make a significant difference in your bottom line. As you move through this article, you’ll discover how the right agriculture casting solutions help minimize downtime, control costs, and drive long-term success in the field.
What Exactly Are Agricultural Castings?
Ever wondered why so many critical farm machinery parts are made using casting instead of other methods? If you’ve examined a heavy-duty tractor component or a precision planter bracket, chances are you’ve seen the results of agricultural casting up close. But what sets this process apart, and why is it so widely used in cast agriculture?
Defining Agricultural Castings
At its core, an agricultural casting is a metal part produced by pouring molten metal into a custom-shaped mold, then allowing it to solidify. This approach makes it possible to create everything from simple housings to intricate gearboxes and levers used across modern farm machinery. Unlike parts that are cut or machined from solid blocks, castings are shaped directly in the mold, allowing for remarkable design flexibility and material efficiency.
Why Casting Is Preferred for Farm Equipment
So, why do manufacturers turn to casting for so many agricultural components? The answer comes down to the unique advantages this process offers—especially when compared to alternatives like forging or fabrication. Here’s what you’ll notice:
Complex Geometries: Casting makes it easy to produce parts with intricate shapes, internal cavities, or hollow sections that would be difficult, if not impossible, to achieve with machining or forging. Think of complex housings or multi-functional brackets—casting handles these with ease.
Strength and Wear Resistance: Agricultural castings are known for their high compressive strength and ability to withstand constant vibration, impact, and abrasive conditions. This is crucial for components exposed to soil, rocks, and tough fieldwork.
Cost-Effectiveness for Production Volumes: Casting is especially economical for low to medium production runs, thanks to lower tooling costs and the ability to produce parts quickly and efficiently. This is ideal for the diverse and sometimes custom needs of agricultural equipment manufacturers.
Material Versatility: The process supports a broad range of metals and alloys, allowing designers to select the best material for each application, whether it’s iron, steel, or aluminum.
How Does Casting Compare to Forging and Fabrication?
When evaluating manufacturing options, it’s helpful to know how casting stacks up against other methods:
Forging: This process involves pressing or hammering metal into shape, which can produce extremely strong parts due to the refined grain structure. However, forging is less suitable for complex or hollow designs and often requires more expensive tooling for intricate shapes. It’s typically chosen for parts where maximum strength is the top priority, such as critical drive shafts or axles.
Fabrication: Fabrication joins metal pieces using welding, cutting, or assembling pre-formed shapes. While flexible for custom builds, it generally can’t match the consistency, surface finish, or geometric complexity of castings.
In short, casting shines when you need complex designs, reliable strength, and cost-effective production—making it the go-to choice for many agricultural machinery parts. As you explore the next section, you’ll see how the choice of materials further enhances the performance and longevity of agricultural castings.
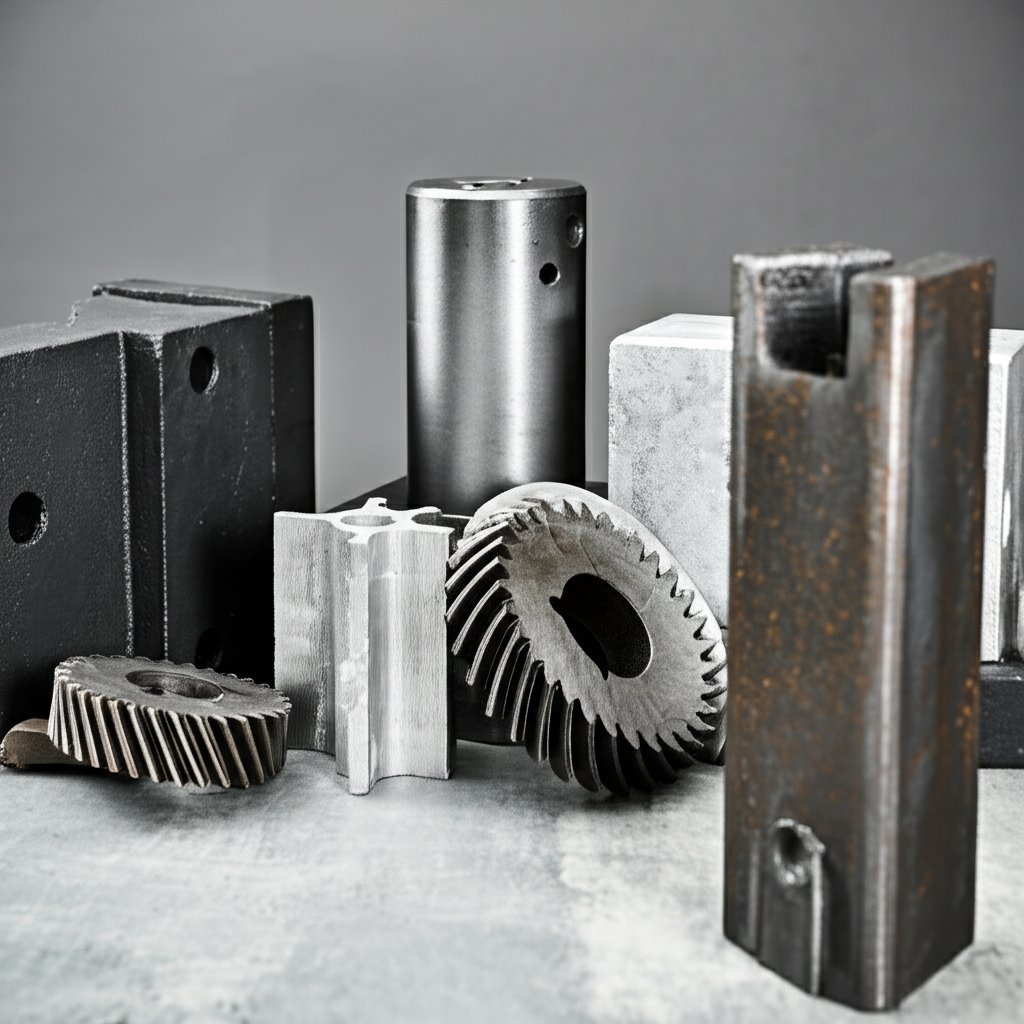
Common Materials Used for Farm Equipment Castings
When you’re evaluating the strength and durability of agricultural castings, have you ever wondered what materials make the difference between a part that lasts one season and one that endures for years? The answer lies in the careful selection of metals and alloys—each chosen for its unique properties and how well it stands up to the rigors of modern farming. Let’s break down the main materials used for agricultural cast iron parts and other key components, so you can see how each one impacts performance and cost.
Key Materials and Their Role in Agricultural Castings
Choosing the right material isn’t just about meeting a spec sheet—it’s about matching the part’s function to the demands of its environment. Here’s a closer look at the most common options for agriculture machinery parts metal casting:
Ductile Iron (Nodular Cast Iron): Known for its impressive strength and flexibility, ductile iron is a top choice for parts that need to absorb shock and resist breaking under heavy loads. Unlike traditional cast iron, its unique microstructure gives it superior toughness, making it ideal for axle supports, brackets, and components exposed to constant vibration or impact. Its cost-effectiveness also makes it a favorite for large, high-stress parts.
Grey Iron: This classic material is widely used for agricultural cast iron parts such as gearboxes, housings, and brake drums. Grey iron stands out for its excellent machinability, vibration damping, and wear resistance—qualities that help reduce noise and extend the life of moving parts. It’s also more affordable than many alternatives, making it a practical choice for high-volume or less critical components.
Cast Steel (Carbon and Alloy Steels): When maximum strength and impact resistance are required, cast steel for agricultural machinery comes into play. Carbon steel grades like 1020 and 8620 offer a balance of toughness and machinability, while alloy steels such as 4130 and 4140 add enhanced tensile strength and durability. These materials are commonly used in gear castings, levers, pivots, and field equipment that must withstand extreme loads or harsh conditions.
Aluminum Alloys: Need to reduce weight without sacrificing strength? Aluminum alloys are increasingly used for certain agricultural machinery parts steel casting applications where corrosion resistance and lighter weight are priorities—think covers, housings, and parts where easy handling is important. While not as strong as steel or iron, aluminum’s resistance to rust and its ease of casting make it an attractive option for non-structural components.
Other Specialty Alloys: In some cases, brass, bronze, or stainless steels are used for specific needs—such as corrosion resistance in valves or fittings, or for parts that demand unique mechanical properties. These materials may carry a higher price tag but deliver targeted performance where it counts.
How Material Choice Impacts Performance and Cost
Imagine you’re selecting a bracket for a tractor: If you choose ductile iron, you get a part that can flex under load without cracking. Opt for grey iron, and you benefit from vibration damping and lower cost, but with less flexibility. For a heavy-duty gear or lever, cast steel offers unmatched strength, though it may come at a higher price. Aluminum, meanwhile, is perfect for covers or housings where weight savings and corrosion resistance are more important than brute strength.
In short, the right material ensures your agricultural castings deliver the durability, reliability, and value your operation demands. As you’ll see in the next section, the manufacturing process—whether investment or sand casting—further enhances how these materials perform in the field.

Investment Casting versus Sand Casting in Agriculture
When you’re sourcing parts for farm machinery, have you ever wondered why some components are sleek and finely detailed while others are rugged and robust? The answer often comes down to the casting process behind each part. Two of the most widely used methods for producing agricultural castings are investment casting and sand casting. But how do you decide which one is right for your needs—especially when precision, durability, and cost are all on the line?
Understanding the Two Main Casting Processes
Investment casting—sometimes called the "lost wax" method—creates highly detailed, precise parts by forming a wax model and encasing it in a ceramic shell. Once the wax is melted away, molten metal fills the shell, yielding components with excellent surface finish and tight tolerances. On the other hand, sand casting uses compacted sand molds to form parts, making it a go-to for larger, simpler shapes and projects where cost-effectiveness is key.
Side-by-Side Comparison: Investment Casting vs. Sand Casting
Feature | Investment Casting | Sand Casting |
---|---|---|
Tolerance & Precision | High (CT 4-6); excellent for detailed, thin-walled parts | Moderate (CT 10-13); best for less complex, thicker parts |
Surface Finish | Smooth, minimal finishing required | Rougher, may need additional machining or grinding |
Design Complexity | Handles intricate shapes, internal cavities, and fine details | Limited by mold design; best for basic geometries |
Tooling/Mold Cost | Higher upfront due to detailed molds and patterns | Lower cost; sand molds are easy and affordable to produce |
Per-Unit Cost (at Scale) | Cost-effective for medium to high volumes; higher for small runs | Very cost-effective for low to high volumes, especially for large parts |
Production Volume | Ideal for medium to large production runs | Flexible—suitable for both small and large batches |
Typical Agricultural Applications | Precision gears, brackets, levers, housings, and agricultural machinery parts investment casting parts | Axle supports, housings, brake drums, large brackets, and basic structural components |
Material Options | Wide range—including steel, iron, stainless, and specialty alloys | Very broad—iron, steel, aluminum, and more |
Lead Time | Longer (due to mold preparation and process steps) | Shorter (sand molds are quick to make and recycle) |
How to Decide: Matching Process to Your Needs
Choose investment casting when you need precision, smooth surfaces, or complex shapes—think of smaller gears, intricate levers, or custom brackets where accuracy matters most. This process is especially valuable for agriculture investment castings that must meet tight tolerances or have thin walls.
Opt for sand casting when you’re producing large, simple parts—like housings, axle supports, or brake drums—where cost and speed are priorities. Sand casting is also flexible for both low and high production volumes, making it a staple for many agricultural foundries.
Imagine you’re designing a new planter frame: If you need detailed features or a net-shape part with minimal machining, investment casting may be the best fit. But if you’re after a robust housing or large bracket at scale, sand casting likely offers the best value.
Both processes have their place in modern agriculture, and the right choice often depends on your part’s function, required tolerances, and production goals. As you move forward, understanding these differences will help you select the process that aligns with your equipment’s needs—and your bottom line. In the next section, we’ll look at how these castings are integrated into a wide range of modern farming machinery, highlighting their essential roles across different equipment types.
Key Casting Applications in Modern Farming Machinery
Ever looked at a tractor or combine and wondered what makes these machines tough enough to handle season after season in the field? The answer is often hidden in plain sight: cast metal components. Agricultural castings are the backbone of countless machines, quietly delivering strength, precision, and longevity where it matters most. But where exactly are these cast parts used, and why are they so indispensable across today’s diverse range of farm equipment?
Where Do Castings Power Modern Agriculture?
Let’s break down the main types of agricultural machinery and see how agricultural machinery casting parts are integrated into each. You’ll notice that castings aren’t limited to just one area—they’re everywhere, from the engine to the implements. Here’s a closer look at the versatility of agriculture equipment castings across key machinery categories:
Tractors
Engine blocks and cylinders: Provide the core strength and heat resistance needed for reliable operation.
Gearbox and transmission housings: Protect gears and internal mechanisms from dust, debris, and impact.
Axle supports and frames: Bear heavy loads and maintain structural integrity on rough terrain.
Hydraulic pump bodies and valve housings: Ensure smooth lifting and control of implements.
Mounting brackets and linkage arms: Connect and secure implements or attachments.
Harvesting Equipment (Combines, Forage Harvesters, etc.)
Guide rails and driving wheels: Direct and transmit motion within the machine.
Rollers and shells: Form the moving parts that separate and process crops.
Threshing drum housings and end covers: Protect internal mechanisms and maintain alignment.
Grain tank and elevator components: Support and move harvested grain efficiently.
Tillage Equipment (Plows, Cultivators, Harrows)
Plowshares and cultivator points: Penetrate soil and resist abrasion in harsh conditions.
Rototiller tines: Break up soil and prepare seedbeds.
Hardware and mounting brackets: Attach tools and implements securely to frames.
Wear liners and blade holders: Extend the lifespan of tillage tools exposed to rocks and debris.
Seeding & Planting Equipment
Seed drill frames and row units: Support precise seed placement and depth control.
Planter hoppers and covers: Protect seeds and mechanisms from contamination.
Disc openers and bearing housings: Cut through soil and maintain alignment during operation.
Mounting arms and brackets: Enable flexible adjustment and secure attachment to toolbars.
Why Are Castings Essential in These Applications?
Imagine the wear and tear faced by a plowshare cutting through stony ground, or a gearbox that must transmit power day after day. Casting agriculture machinery allows manufacturers to tailor each part’s material and design to its specific function, combining strength, wear resistance, and precise fit. The result? Equipment that lasts longer, performs better, and keeps maintenance costs in check.
It’s not just about durability—agricultural casting equipments also enable complex shapes and internal features that would be impossible or prohibitively expensive with other manufacturing methods. That means smoother operation, better integration with other parts, and more efficient farming overall.
As you can see, castings are integral to every stage of the farming process, from soil preparation to harvest. In the next section, we’ll explore how these cast parts are specially engineered for the most demanding roles, such as ground-engaging tools in tillage and seeding equipment, where durability and performance are absolutely critical.
Essential Cast Components for Tillage and Seeding Equipment
When you picture a plow slicing through rocky soil or a seeder working dawn to dusk, you might wonder—what keeps these ground-engaging tools performing season after season? The answer lies in the specialized agricultural machinery parts casting that form the backbone of tillage and seeding equipment. Let’s break down why these cast parts are so vital, what stresses they endure, and which components are most critical to reliable field performance.
Why Casting Is Crucial for Ground-Engaging Parts
Sounds complex? It is. Tillage and seeding parts face some of the harshest conditions in agriculture. Every pass through the field means repeated abrasion from soil, sand, and rocks, along with sudden impacts from hidden debris. These stresses can quickly wear down lesser components, leading to costly downtime and frequent replacements. That’s why casting—especially with carefully selected iron or steel alloys and advanced heat treatments—is the go-to solution for high-wear applications. Casting allows for:
Custom shapes and reinforcements: Complex geometries that maximize strength where it’s needed most.
Material optimization: Use of high-hardness alloys and tailored heat treatments for maximum wear and impact resistance.
Consistent quality: Repeatable manufacturing processes that deliver reliable performance, batch after batch.
Imagine swapping out a plow point midway through planting season—every delay means lost productivity. By using cast parts engineered for extreme durability, you minimize those risks and keep your operation on schedule.
Critical Cast Components in Tillage and Seeding
Let’s look at the key agricultural casting parts that make the difference in field performance. Each is designed to withstand specific stresses and extend service life, even in the toughest soils:
Plow Points and Shovels: These are the first line of contact with the soil, cutting and turning earth. Cast from high-strength steel or ductile iron, they must resist constant abrasion and occasional impacts from rocks. Many feature hardened edges or overlays for extra longevity.
Sweeps and Cultivator Points: Designed for soil aeration and weed control, these parts need both sharpness and toughness. Cast sweeps often have reinforced ribs and are heat-treated for optimal hardness.
Disc Blades and Hubs: Used to slice through residue and mix soil, disc blades are subject to tremendous abrasive wear. Cast hubs provide the structural support needed to handle shock loads and maintain alignment.
Planter Row Unit Frames: These frames support seed metering and placement mechanisms. Cast construction ensures they can handle vibration, twisting, and repeated impacts without deforming.
Seed Firmers and Press Wheels: While less exposed to direct abrasion, these components still require strength and dimensional accuracy to ensure proper seed-to-soil contact and consistent planting depth.
What Makes a Cast Part Las?
It’s not just about the base material. The best agriculture machinery parts casting combine:
Material selection: Ductile iron for shock absorption, high-carbon steel for abrasion, or alloyed castings for a balance of properties.
Heat treatment: Processes like quenching and tempering to boost hardness and toughness.
Precision manufacturing: Tight control of casting and machining tolerances for perfect fit and function.
Quality foundries may also apply surface treatments or overlays to further extend wear life, especially on leading edges and high-contact zones.
In summary, the cast components used in tillage and seeding equipment are engineered to thrive where lesser parts would fail. Their design, material, and manufacturing process are all chosen to maximize uptime and minimize maintenance—keeping your fields productive and your equipment running strong. Next, we’ll take a closer look at the step-by-step journey these castings take from design to finished product, so you can better appreciate the expertise and quality control behind every reliable part.
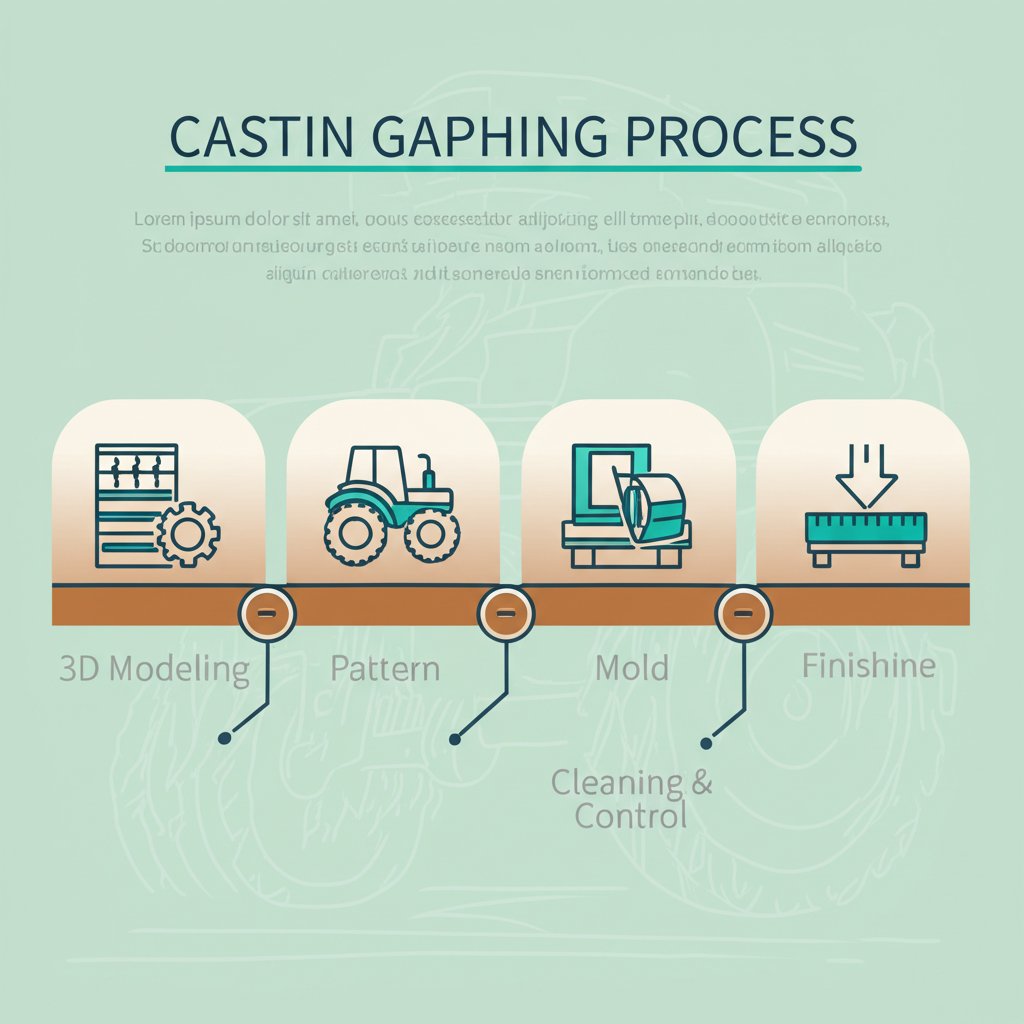
The Manufacturing Journey of an Agricultural Cast Part: From Design to Durable Performance
Ever wondered how a rugged gearbox housing or a precision planter bracket goes from a design sketch to a finished, field-ready component? The path from idea to reliable agricultural casting products is more intricate than it might appear. Each step, from pattern design to final inspection, is engineered to maximize quality and ensure every part stands up to the demands of modern farming. Let’s walk through this journey, so you can better appreciate the expertise and attention to detail that goes into every cast part.
Step 1: Design Review & Pattern/Tooling Creation
It all begins with a detailed review of the part’s requirements—dimensions, material, operating stresses, and fit with other machinery. Experienced engineers collaborate with customers to optimize the design for casting. This includes considering draft angles, wall thickness, and material flow. Once finalized, a pattern (the model of the part) is created. For sand casting, patterns may be made from wood, plastic, or metal, while investment casting uses wax or plastic patterns.
Why it matters: Accurate patterns set the foundation for dimensional precision and repeatability in every casting.
Step 2: Mold Making
Next, the pattern is used to create a mold—the cavity that will shape the molten metal. In sand casting, sand mixed with binders is packed around the pattern to form the mold. For investment casting, the wax pattern is coated with ceramic slurry and then hardened to form a shell. Cores may be added to create internal cavities or complex features.
Why it matters: Mold quality directly affects surface finish, dimensional accuracy, and the ability to cast complex geometries.
Step 3: Metal Melting & Pouring
With the mold ready, it’s time to melt the selected metal—whether ductile iron, steel, or aluminum alloy. The furnace type and melting process are chosen based on the metal and desired properties. Once molten, the metal is poured into the mold cavity. Pouring must be controlled for temperature and speed to ensure complete filling and minimize defects.
Why it matters: Precise melting and pouring are critical for achieving the right microstructure and avoiding internal flaws.
Step 4: Shakeout & Cleaning
After cooling and solidification, the mold is broken away (in sand casting) or the ceramic shell is removed (in investment casting), revealing the rough casting. Excess sand, ceramic, and gating systems are cleaned off through vibration, blasting, or washing. This is called the shakeout process.
Why it matters: Proper cleaning ensures no foreign material remains, which could compromise the part’s function or longevity.
Step 5: Heat Treatment
Depending on the application, the casting may undergo heat treatment—such as annealing, normalizing, or quenching and tempering—to refine its mechanical properties. This step enhances hardness, toughness, and wear resistance, tailoring the part for its intended use.
Why it matters: Heat treatment is essential for optimizing strength and durability, especially for high-stress agricultural casting products.
Step 6: Finishing & Machining
Once the casting has the desired properties, it’s time for finishing. This may include grinding, machining, drilling, or surface treatments to meet precise dimensional and surface finish requirements. Some parts are ready after minimal finishing, while others require tight tolerances and further processing.
Why it matters: Finishing ensures each part fits perfectly in its assembly and operates smoothly in the field.
Step 7: Quality Inspection & Testing
The final—and perhaps most critical—step is quality control. Each casting is inspected for dimensional accuracy, surface finish, and internal soundness. Techniques may include visual inspection, coordinate measuring machines (CMM), ultrasonic or X-ray testing, and hardness or tensile testing. Only parts that meet strict standards move on to packaging and shipment.
Why it matters: Rigorous inspection catches defects early, ensuring only reliable, high-performance agricultural casting products reach the customer.
Why Every Step Counts
Imagine skipping a step or cutting corners—what would happen if a mold wasn’t made precisely, or a casting wasn’t properly heat-treated? The result could be premature wear, unexpected failure, or costly downtime in the middle of planting or harvest. That’s why reputable foundries invest in skilled teams, advanced equipment, and robust quality systems at every stage of production.
In summary, the journey from design to finished agricultural casting is a careful blend of engineering, craftsmanship, and quality control. Each part is shaped not just by metal and molds, but by the expertise and commitment of the team behind it. As you consider your next supplier, understanding this process will help you appreciate the value of proven manufacturing excellence. Up next, we’ll explore what to look for when selecting a casting supplier—so every component you source is built to last.
Choosing the Right Agricultural Casting Manufacturer
When you’re sourcing critical components for your agricultural equipment, the choice of supplier can make or break your operation’s reliability and bottom line. Sounds complex? It can be—especially with so many agricultural casting parts suppliers promising quality and performance. So, how do you separate the truly dependable from the rest? Let’s break down the essential factors you should consider before partnering with an agricultural casting manufacturer.
What Should You Look for in a Supplier?
Imagine placing a large order for gearbox housings or tillage blades, only to find the parts don’t meet your specs or arrive weeks late. To avoid costly disruptions, here’s a practical checklist of criteria that can help you identify a reliable partner:
Industry Experience: Does the supplier have a proven track record in agricultural castings? Years of experience often translate into deep process knowledge and a better understanding of the unique demands of farm machinery. Suppliers with a diverse client base in agriculture are more likely to anticipate and address your specific needs.
Material Expertise: Can the foundry offer a broad range of materials—like ductile iron, cast steel, and aluminum alloys—tailored to your application? The best suppliers help you select the optimal material for each part, balancing cost, durability, and performance. Ask for examples of previous projects that match your requirements.
Casting Process Capabilities: Does the manufacturer support multiple casting methods (sand, investment, lost-foam, die casting, etc.)? This flexibility means your components can be matched to the most efficient and cost-effective process, whether you need high-volume runs or complex geometries.
Quality Management Systems: Look for evidence of robust quality assurance—such as ISO 9001 or similar certifications. Reliable suppliers maintain strict process controls, regular inspections, and documented testing at every stage of production, ensuring every batch meets your specs.
In-House Heat Treatment & Machining: Does the foundry offer integrated heat treatment and machining? This can streamline your supply chain and ensure that castings arrive ready for assembly, with the required mechanical properties and dimensional accuracy.
Technical Support & Engineering Collaboration: Can the supplier assist with design optimization, prototyping, and troubleshooting? Access to experienced engineers helps you refine part geometry, choose the right alloys, and solve problems before they impact production.
Production Capacity & Scalability: Is the manufacturer equipped to handle your current order size—and scale up if your needs grow? Flexible capacity is crucial for meeting seasonal demand spikes or expanding product lines.
Testing & Inspection Facilities: Does the supplier have advanced labs and equipment for non-destructive testing, dimensional checks, and material analysis? On-site testing ensures defects are caught early, protecting your reputation and reducing risk.
Customer References & Reputation: Ask for references from similar projects or industries. A reputable supplier will gladly share testimonials and case studies that demonstrate their reliability and service quality.
Transparent Communication & Logistics: How responsive is the supplier? Clear timelines, proactive updates, and reliable shipping arrangements help you avoid surprises and keep your operations running smoothly.
Why These Factors Matter
Choosing a supplier isn’t just about price or proximity—it’s about building a partnership that delivers consistent quality, on-time delivery, and technical support when you need it most. For example, a supplier with in-house heat treatment and advanced testing facilities can catch and correct issues before they reach your assembly line, saving you time and money. Likewise, a company with deep material expertise can recommend alloys or casting processes that extend the life of your equipment, reducing long-term maintenance costs.
What Sets a Top Supplier Apart?
The best agricultural casting parts suppliers invest in continuous improvement, adopt the latest manufacturing technologies, and maintain close communication with customers. They understand the pressures of planting and harvest windows, offering flexible production schedules and fast turnaround to minimize downtime. Strong partnerships are built on transparency, technical know-how, and a shared commitment to operational success.
As you evaluate your options, remember: the right supplier isn’t just a vendor—they’re a strategic ally in your drive for reliable, high-performance farm equipment. In the next section, we’ll dive deeper into the specific quality factors you should insist on to ensure your agricultural castings stand the test of time and deliver lasting value.
Quality Factors for Long Lasting Agricultural Castings
When you invest in new farm machinery, you expect every component to go the distance. But what actually makes high-quality agricultural castings stand up to years of hard work? Sounds complex? It can be—especially when you consider the tough environments these parts face. Let’s break down the essential quality factors that separate dependable castings from those that cause costly breakdowns and downtime.
What Should You Look for in a High-Quality Agricultural Casting?
Imagine a gearbox housing that cracks mid-season or a tillage point that wears out after just a few passes. These failures often trace back to overlooked quality attributes. Here’s what savvy buyers and engineers focus on to ensure castings deliver long-lasting performance:
Material Integrity: The foundation of any quality casting is the right material, verified through rigorous testing. This means using alloys with the proper chemical composition and purity, ensuring the casting can resist wear, corrosion, and impact. Reliable suppliers conduct chemical analysis and mechanical testing to confirm every batch meets specifications.
Dimensional Accuracy: Precision matters—parts that are even slightly out of spec can cause misalignment, premature wear, or assembly headaches. Look for castings produced with tight tolerances, verified by coordinate measuring machines (CMM) or other advanced inspection tools. This ensures a perfect fit and smooth operation in the field.
Surface Finish: A smooth, defect-free surface isn’t just about appearance. It reduces friction, minimizes stress concentrations, and helps prevent cracks or corrosion. High-quality agricultural castings are free from surface defects like pits, roughness, or residual sand, thanks to careful mold making and finishing processes.
Mechanical Properties (Hardness, Strength, Toughness): Depending on the part’s function, you’ll want castings with the right balance of hardness (for abrasion resistance), strength (to handle heavy loads), and toughness (to absorb shock without cracking). Heat treatment is often used to fine-tune these properties, ensuring parts perform reliably under real-world stresses.
Consistency and Repeatability: Ever had one batch of parts perform well, then the next batch fails early? Consistency is key. Top foundries use robust quality control systems—like ISO 9001 certifications—and set up critical control points throughout production to guarantee every casting meets the same high standards, every time.
How Do These Factors Reduce Downtime and Costs?
Think about the ripple effect of a single casting failure: repair costs, unplanned downtime, lost productivity, and potential crop losses. By insisting on quality attributes like those above, you directly reduce these risks. High-integrity materials and accurate dimensions mean parts fit and function as designed. Superior surface finish and mechanical properties translate to longer wear life and fewer replacements. Consistent quality ensures you can trust every shipment, not just the first one.
"Quality control isn’t just about passing inspection—it’s about delivering reliable performance in the field, season after season."
Best Practices for Ensuring Quality
Specify material and mechanical property requirements in your purchase orders.
Request material certifications and inspection reports with each batch.
Work with suppliers who implement advanced testing—such as X-ray, ultrasonic, or CMM inspections—to catch defects early.
Partner with foundries that follow recognized quality management systems and continuously invest in process improvement.
When you prioritize these quality factors, you’re not just buying a part—you’re investing in fewer breakdowns, lower maintenance costs, and greater peace of mind. As we wrap up, you’ll see how these principles tie into supplier selection and the long-term reliability of your agricultural equipment.
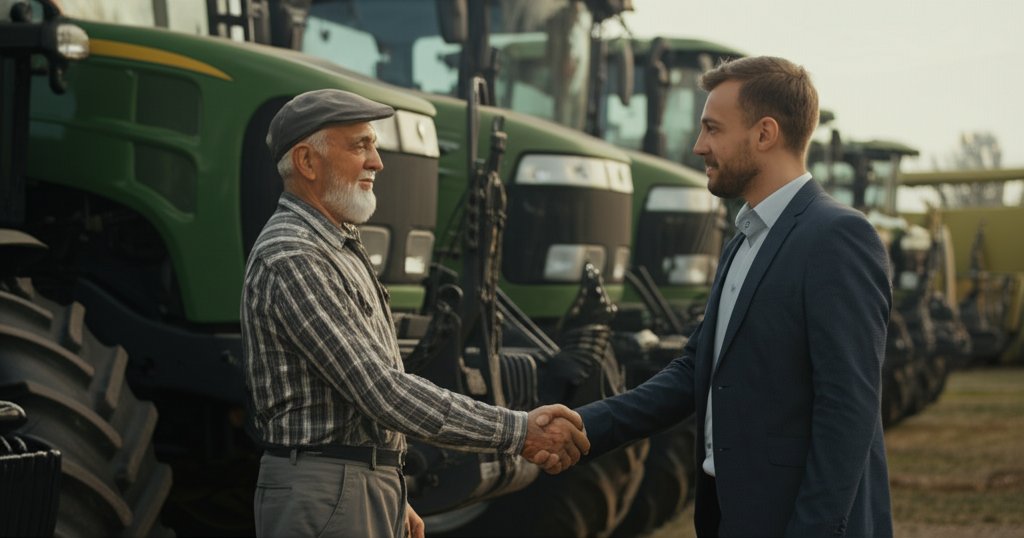
Conclusion
Reliable Agricultural Casting Supplier—The Foundation of Modern Farming Success
When you look back at the journey from raw metal to field-proven machinery, it’s clear that agricultural castings are more than just components—they’re the foundation of reliable, productive, and cost-effective farming. Every gearbox housing, tillage blade, and axle support produced through advanced casting processes helps keep tractors, harvesters, and implements running strong, season after season.
But here’s the key question: how do you ensure your equipment delivers that reliability year after year? The answer goes beyond just material selection or manufacturing process. It comes down to partnering with a reliable agricultural casting supplier who understands the unique challenges of the agricultural sector and has the expertise to deliver consistent, high-quality results.
What Sets a Top Supplier Apart?
Comprehensive Solutions: The best suppliers offer a full spectrum of casting processes—sand, investment, lost-foam, die, and more—so every component is matched to its ideal method and material. This flexibility ensures you get the right balance of durability, weight, and cost for each application.
Material and Process Expertise: Top manufacturers guide you in choosing between ductile iron, cast steel, aluminum alloys, and specialty materials, optimizing each casting for its real-world environment. Their experience means fewer surprises and longer-lasting parts.
Advanced Technology and Rigorous Quality Control: Reliable partners invest in state-of-the-art production lines, non-destructive testing, and in-house machining. This attention to detail means every batch of agricultural castings for OEMs meets exacting standards for fit, finish, and mechanical properties.
Customization and Rapid Turnaround: The ability to tailor designs, alloys, and delivery schedules allows you to minimize downtime, control inventory, and respond quickly to changing field demands.
Industry Recognition and Support: Leading suppliers are recognized for their quality and service, offering technical support, robust logistics, and a commitment to long-term partnership—not just one-off sales.
Why TIEGU Stands Out as a Casting Partner
Imagine having all these advantages under one roof. TIEGU exemplifies what today’s agricultural equipment manufacturers and large-scale growers need from a casting supplier. With a wide range of casting technologies, deep material science expertise, and a proven track record serving OEMs and rebuilders, TIEGU delivers:
Durable, high-performance castings engineered for abrasive soils, moisture, and heavy loads
Custom solutions that match geometry, alloy, and production volume to your exact requirements
Fast turnaround and manageable tooling costs to keep your projects on schedule and budget
Comprehensive in-house quality control, including non-destructive testing and precision machining
Global support and industry recognition for reliability and innovation
By choosing a partner like TIEGU, you’re not just buying parts—you’re investing in uptime, lower maintenance costs, and the long-term reputation of your equipment.
Take Action: Prioritize Quality and Partnership
As you move forward with your next project or procurement cycle, remember: the true value of agricultural castings is realized only when they’re sourced from a supplier who meets the highest standards for quality, customization, and service. Don’t settle for the lowest bidder or a one-size-fits-all approach. Instead, seek out a supplier who will work with you as a partner—one who understands your goals, anticipates challenges, and delivers solutions that drive your business forward.。
Ready to experience the benefits of a truly reliable agricultural casting supplier? Contact TIEGU to discuss your needs and discover how the right casting partnership can transform your equipment’s performance, reliability, and bottom line.
Frequently Asked Questions about Agricultural Castings
1. What is casting in agriculture?
Casting in agriculture refers to the process of shaping metal parts by pouring molten metal into molds. This method is essential for producing durable and complex components used in farm machinery, such as housings, brackets, and gearboxes. The process allows for customization and optimal strength, helping equipment withstand harsh field conditions and reducing downtime.
2. Why are castings important for farm equipment?
Castings are crucial because they provide the strength and wear resistance needed for agricultural machinery to operate reliably in tough environments. High-quality agricultural castings help minimize machine breakdowns, extend equipment lifespan, and lower long-term maintenance costs—directly impacting farm productivity and profitability.
3. What materials are commonly used for agricultural castings?
Common materials include ductile iron, grey iron, cast steel, and aluminum alloys. Each material is selected based on its ability to handle specific stresses, such as abrasion or impact, and its suitability for the intended application. The right choice ensures optimal performance, durability, and cost-effectiveness for farm machinery parts.
4. How do I select a reliable agricultural casting supplier?
Look for suppliers with proven industry experience, expertise in various casting materials and processes, robust quality management systems, in-house heat treatment and machining, and strong customer support. Companies like TIEGU excel by offering comprehensive casting solutions, advanced technology, and customization options to meet diverse agricultural needs.
5. What are the main differences between investment casting and sand casting in agriculture?
Investment casting is ideal for producing precise, detailed parts with smooth finishes, while sand casting is suited for larger, simpler components and offers lower tooling costs. The choice depends on part complexity, required tolerances, production volume, and budget. Both methods play vital roles in manufacturing reliable farm equipment components.