What is Spheroidizing Treatment?
2025-01-02 15:49:41 hits:0
In the casting field, spheroidizing treatment is a core process in the production of ductile iron and plays a crucial part.
Spheroidizing treatment refers to adding specific spheroidizing agents into the liquid iron melt. The amount of addition must be precisely controlled. Through this operation, the flake-like or vermicular graphite in ordinary cast iron will transform into uniformly distributed spherical graphite.
The morphology of graphite has an extremely significant impact on the properties of cast iron.
In ordinary cast iron, the flake graphite, when subjected to external forces, will create stress concentration points inside the material, leading to a remarkable reduction in the strength and toughness of the material. Relevant mechanical test data indicate that the tensile strength of ordinary gray cast iron generally ranges from 200 to 300 MPa, and the elongation is only between 0.3% and 0.8%. After spheroidizing treatment, the spherical graphite is evenly distributed in the iron matrix, which can effectively disperse stress and avoid stress concentration, and thus the strength and toughness of the cast iron are substantially enhanced. The tensile strength of ductile iron can reach 400 - 600 MPa, and the elongation can be increased to 2% - 10%.
Application of Spheroidizing Treatment in the Automotive Industry
Taking the automotive industry as an example, the manufacture of many key components relies on ductile iron after spheroidizing treatment. For engine blocks, when an automotive engine is running, the temperature inside the block can instantaneously soar to over a thousand degrees Celsius, and the pressure will suddenly rise to several megapascals. Moreover, it has to endure high-frequency vibration impacts. A renowned automotive brand made a comparison during its research and development. For an engine with an ordinary cast iron block, after running 100,000 kilometers in a durability test, multiple fine cracks emerged on the block, causing a decline in power performance by approximately 15%. However, after replacing it with a ductile iron block, under the same mileage, the block remained intact and the power output was stable.
The same applies to automotive wheels. When a vehicle is traveling, the wheel not only has to bear the weight of the vehicle body but also withstand the huge centrifugal force generated by high-speed rotation and the impact from road bumps. For instance, in a simulated extreme road condition test, after an ordinary aluminum alloy wheel underwent 500 high-intensity bump impacts, 5 deformations and 2 cracks appeared. In contrast, under the same conditions, the ductile iron wheel only had slight wear and its structure remained intact, demonstrating strong reliability.
Precautions for Using Spheroidizing Agents
In actual operation, the selection and addition amount of spheroidizing agents are of great importance.
Common spheroidizing agents contain elements such as magnesium and rare earths, and different formulations are determined according to specific iron melt compositions and casting requirements. If high-strength mechanical parts are to be cast, spheroidizing agents with a magnesium content of 7% - 10% are usually chosen. If components with high toughness requirements are to be cast, formulations with a slightly higher rare earth content are preferred. If the addition amount is too much, the iron melt will have an overreaction, resulting in defects such as slag inclusions and pores. If the addition amount is too little, the graphite spheroidization will be incomplete. Experienced foundry workers will operate precisely based on the real-time state of the iron melt to ensure a good spheroidizing effect for each furnace of iron melt.
In addition, the timing of spheroidizing treatment is vital.
The iron melt needs to accurately reach a suitable temperature range, with uniform and stable components and after sufficient smelting, before the spheroidizing agents can be added quickly and uniformly to ensure a stable and efficient reaction. Subsequently, an inoculation treatment process must be carried out immediately to further optimize the morphology of graphite spheres, refine the grains, and improve the quality of the cast iron, laying a solid foundation for producing high-quality ductile iron products.
In conclusion, spheroidizing treatment is an important link in modern casting technology. It has opened the door to the wide application of ductile iron, provided high-performance materials for industries such as automobiles, machinery manufacturing, and shipping, and promoted scientific and technological progress and industrial development.
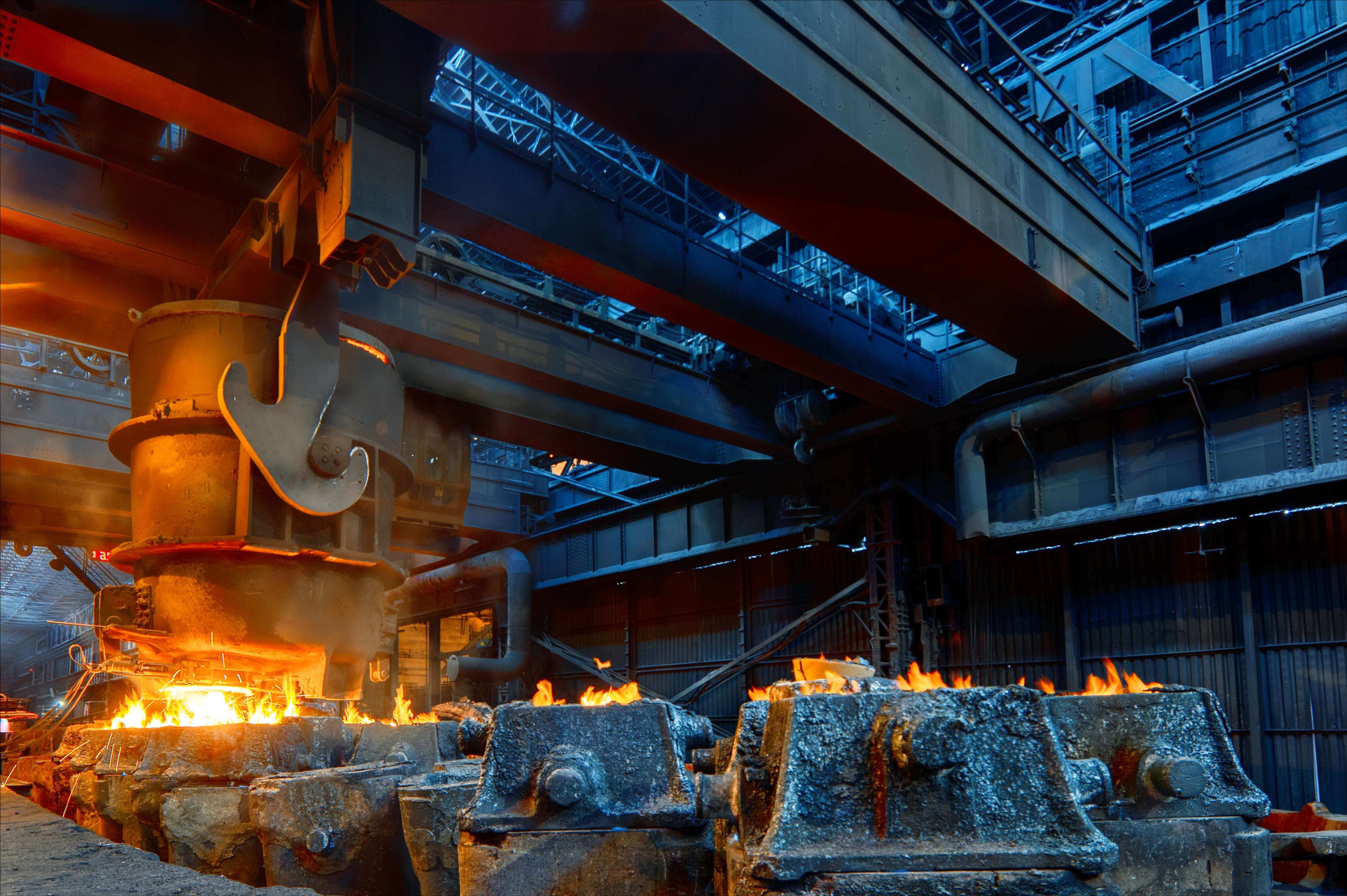